Sustainability
Promote Health and Productivity Management
Indicators and Targets
Our group has identified “promote health and productivity management” as a materiality, and has established the following KPIs to promote initiatives.
Indicators | Scope | Unit | FY2021 | FY2022 | FY2023 | Medium- to Long-term Targets | |
---|---|---|---|---|---|---|---|
FY2024 | FY2030 | ||||||
Number of occupational injuries requiring time off work (absence from work greater than one day) | consolidated (domestic) | cases | 5 | 1 | 0 | 0 | 0 |
Of which, number of occupational injuries requiring time off work (report of worker’s death, injury, or illness) | consolidated (domestic) | cases | 4 | 0 | 0 | 0 | 0 |
Percentage of employees undergoing specified health examinations | consolidated (domestic) | % | 85.9 | 88.9 | 90.3 | 90 | 90 |
Percentage of employees provided specified health guidance | consolidated (domestic) | % | 37.6 | 52.5 | 61.4 | 55 | 60 |
Health Management
We believe that investing in the promotion of our employees' health invigorates our organization by energizing employees and making them more productive. This contributes to the sustainable growth of the Company. Failing to create environments where our employees can continue to work in good health would render the Company incapable of sustainable growth. That is why the Company and our health insurance union are conducting collaborative health* initiatives, closely connecting the Company's health management (investment) and the health insurance union's data health plan activities.
* Companies and health insurance unions each performing their own roles and meeting their own responsibilities while collaborating together to promote the health of employees
Support for the Promotion of Employee Mental and Physical Health
We have created a third phase data health plan as an effective and efficient health promotion project (data health) that uses data analysis to assess the health of employees and their family members and addresses health issues. We are monitoring progress on this plan, making improvements, sharing scoring report information with the health insurance union, and conducting reviews to address and resolve health issues.
We have defined the specific health examinations and specific health guidance participation rate as a key performance indicator (KPI) in our lifestyle-related disease countermeasures, and we are working to raise participation rates. We have adopted periodic health checkups based on comprehensive medical examinations annually for employees aged 40 and older as a disease prevention measure. In addition, we are enriching our efforts to diagnose cancer, including breast cancer. We are also carrying out measures for highrisk employees who have yet to undergo health checkups, conducting diabetes prevention/mitigation and smoking cessation programs, implementing shoulder stiffness and back pain prevention measures, holding “walking challenge” promotion activities, and issuing seasonal magazines and pamphlets to promote health literacy. Through these efforts, we are providing support to help employees change their activity patterns to enjoy mental and physical health.
We are also, of course, conducting stress checks, as specified in the Industrial Safety and Health Act. These stress checks help employees become aware of their own stress and assist them in dealing with them. They also help prevent mental health issues in advance by improving workplace environments. When workplaces are found to have high stress levels, we promptly take steps to make workplace environment improvements.
Ensuring of Work-life Balance
We have created various systems, including a flex time system and a working-hour interval system, to ensure that employees can maintain their work-life balance.
System for Half-day Paid Leave and Period for Promoting the Taking of Paid Leave
Paid leave expires after two years. This system allows paid leave to be withheld and accumulated for up to 60 days. Withheld leave can be taken for taking care of children, nursing care, and for illnesses and injuries not related to work.
System for Accumulating Expired Paid Leave
We have introduced a system where employees can take paid leave for half a day at a time and are conducting campaigns for promoting the taking of paid leave. Other ways in which we are focusing on ensuring work-life balance include the planned taking of annual paid leave, in which we have major periods of consecutive leave with the entire site taking leave together.
Occupational Health and Safety
Fundamental Occupational Health and Safety Policy
Based on our belief that safety comes above all else, we consider occupational health and safety to be one of the most important foundations of our business operations, and strive to maintain and improve our healthy and safe working environments.
Occupational Health and Safety Policy
- Comply with occupational health and safety laws and regulations
- Maintain and improve our occupational health and safety structure
- Create comfortable work environments
- Promote health
Occupational Health and Safety Structure
We carry out our business operations with an occupational safety management system in accordance with ISO 45001.
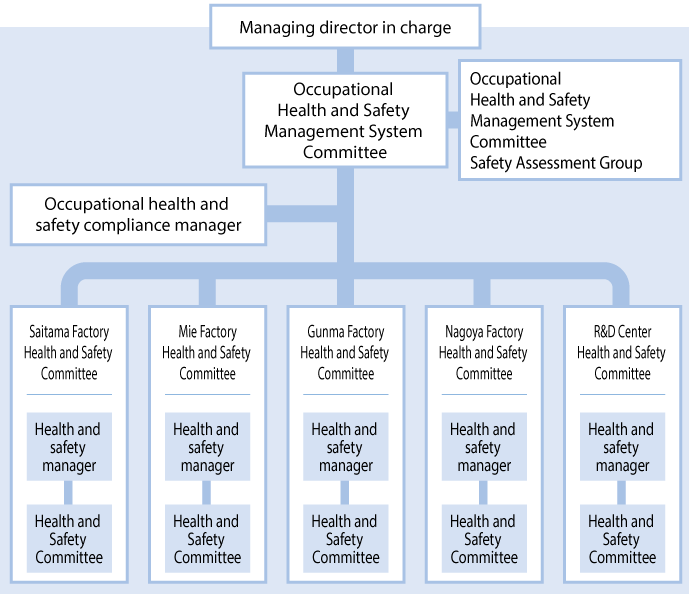
Safety and Health Activities
Activities to Eradicate Causes of Dangers and Hazards through Risk Assessments
Following the introduction of risk assessments in 2003, improvement activities to prevent incidents were established to eliminate and separate potential dangers and hazards in the workplace to reduce risks. Going beyond “zero industrial accidents,” all employees work to achieve “zero risks” by participating in safety awareness and risks and systems improvement activities.
Health and Safety Patrols
Factory managers regularly patrol workplaces to confirm that there are no latent risks or unsafe behavior in factories, and that the 5S are being practiced as fundamental behavior. We perform risk assessments of the hazards identified through these activities, and establish work environments which place safety first.
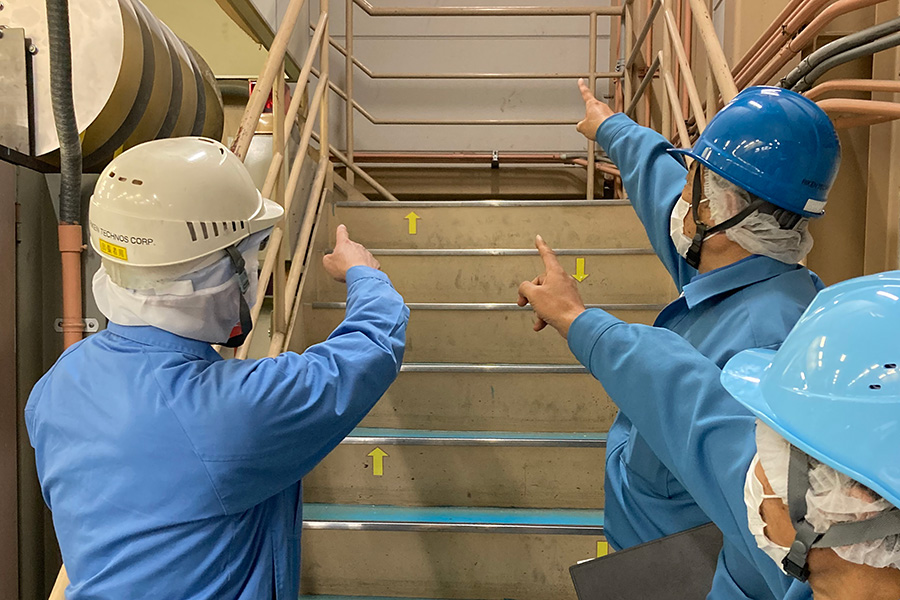
Virtual Reality Safety Education
We have introduced educational contents making use of virtual reality (VR) as part of safety education and kiken yochi training (KYT: hazard prediction training) at work sites involved in dangerous work within our factories. The use of VR allows simulated experiences of industrial accidents and dangerous situations, helping to prevent accidents and improve safety awareness.
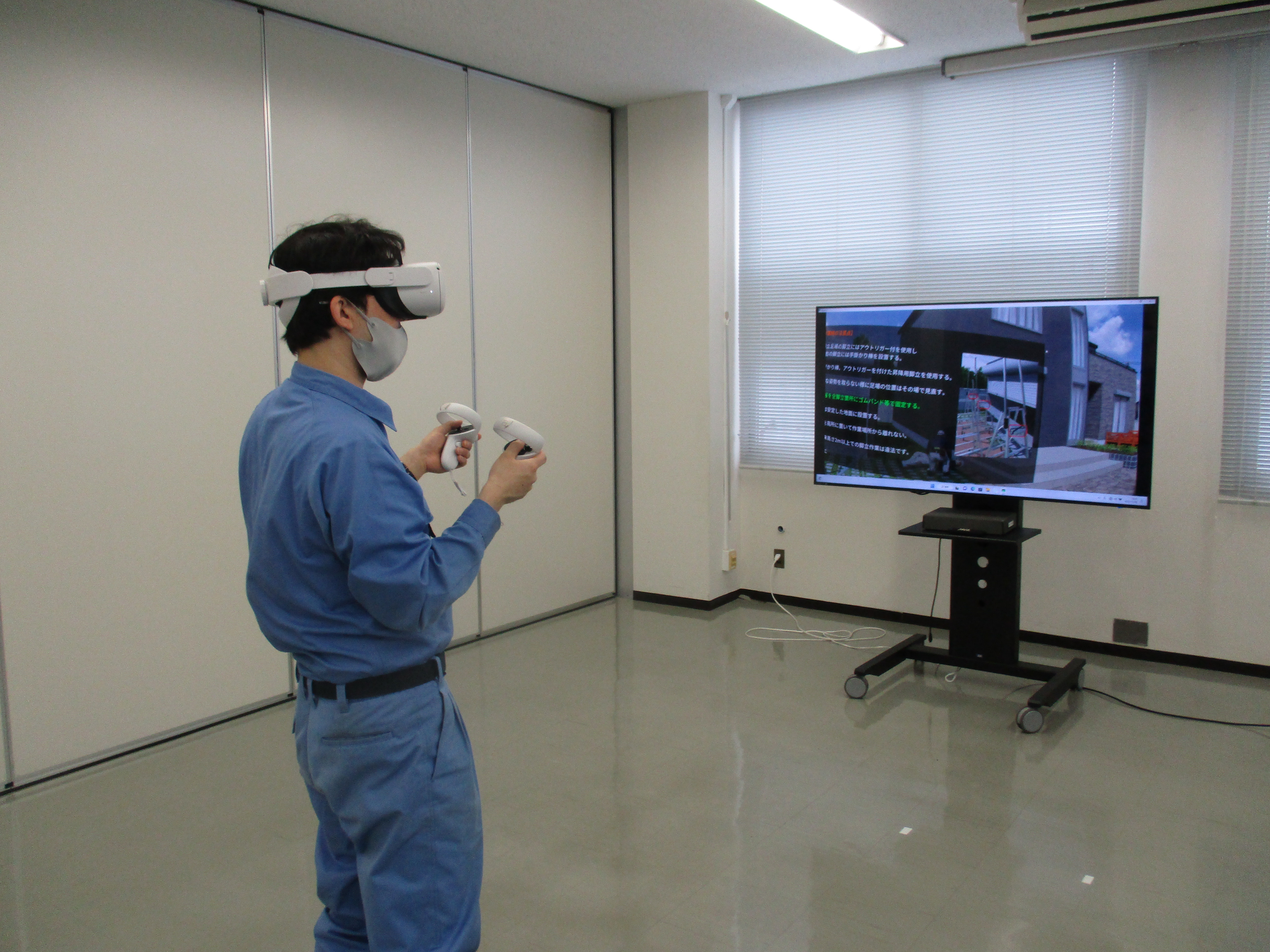
Sharing of Health and Safety Information
Materials regarding health and safety and information regarding industrial accidents are shared between all Group companies, including overseas consolidated subsidiaries. This helps improve the safety awareness of operators and prevent accidents.
Results of Safety and Health Activities
Incidence of Industrial Accidents
Our Group has never had a fatal accident.
SHANGHAI RIKEN TECHNOS CORPORATION
Excellent Company Award
We received an award as an excellent company from the management committee of Shanghai Xinzhuang Industrial Park, where we are located. Following last year, we have received this award for two consecutive years. This award is presented to companies that practice healthy corporate management with no issues in aspects such as safety and the environment.
RIKEN ELASTOMERS CORPORATION
Governor’s Safety and Health Award from State of Kentucky
We received the Governor’s Safety and Health Award from the Commonwealth of Kentucky, where we are located, for our occupational health and safety initiatives. We have received this award for five consecutive years since 2020.
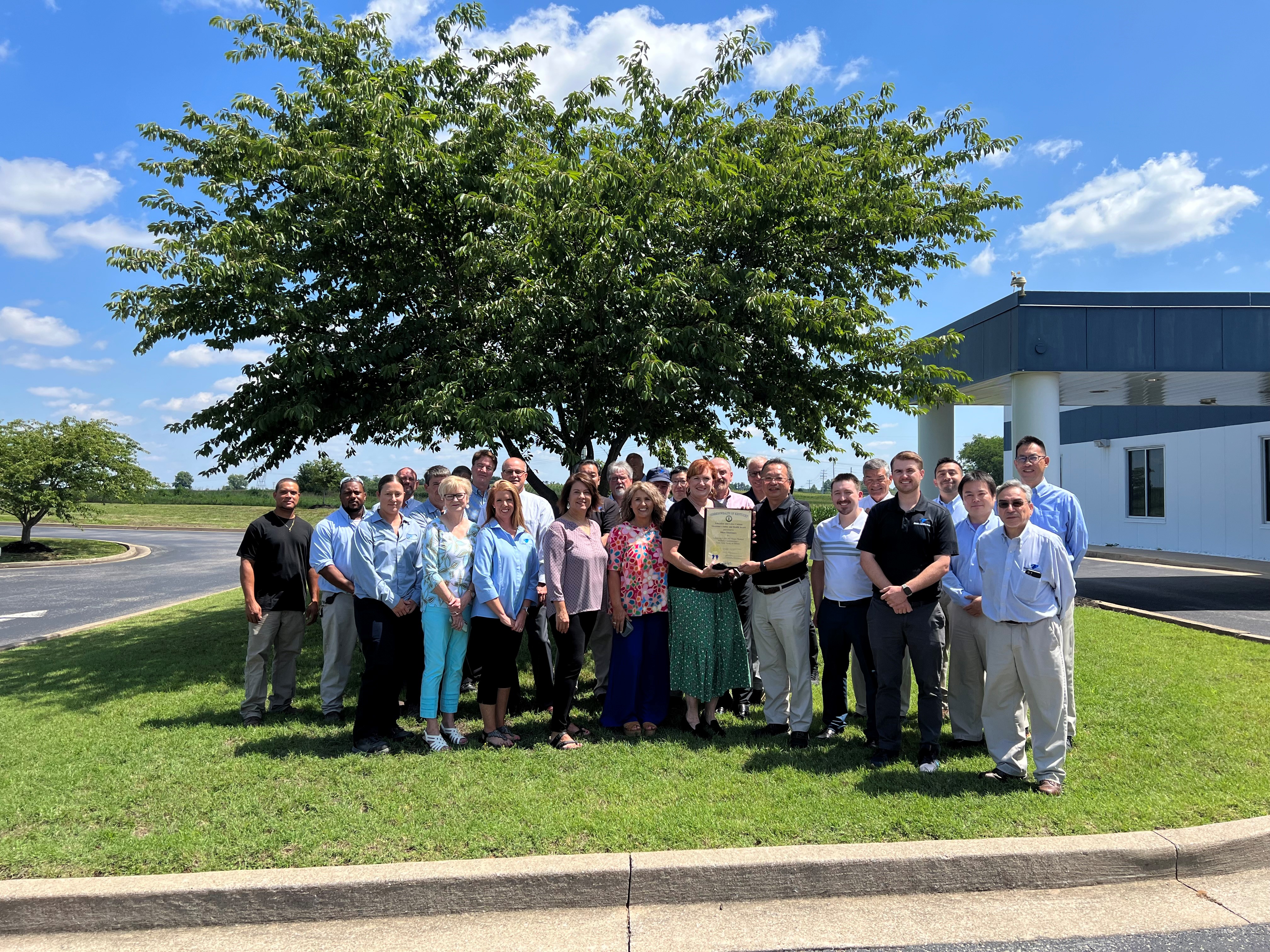