Sustainability
Improve Quality and Ensure of Product Safety
To enhance our Group’s Product Quality Policy “Supply reliable products and services under the concept of Customer-First and Best Quality,” we will review our quality control standards, entrench the RIKEN Standard throughout the Group, and promote the establishment of a global quality assurance structure that pursues automation.
Indicators and Targets
Indicators | Scope | Unit | FY2021 | FY2022 | FY2023 | Medium- to Long-term Targets | |
---|---|---|---|---|---|---|---|
FY2024 | FY2030 | ||||||
Serious quality incidents requiring recalls | non-consolidated | cases | 0 | 0 | 0 | 0 | 0 |
Quality Assurance Structure
Led by our Product Quality Policy “Supply reliable products and services under the concept of Customer-First and Best Quality”, we engage in manufacturing in compliance with ISO 9001. Thorough quality control over entire processes, from acceptance of raw materials to delivery of products, is conducted by carrying out quality improvement activities in collaboration with all of our production sites, including overseas sites, every week. In addition to preventing the reoccurrence of past defects, we perform root cause analysis and share information regarding new defects.
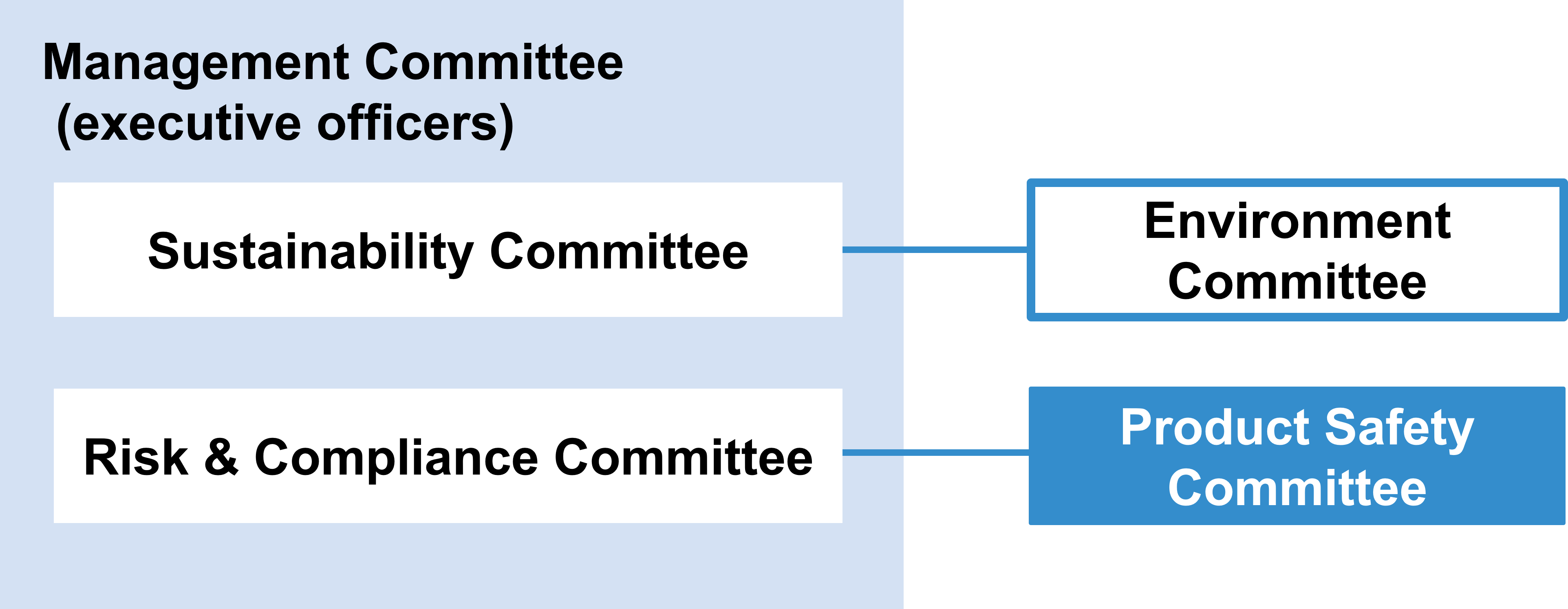
Certification of ISO 9001: 2015
Registration date: September 14, 1998(certification being maintained)
Quality Improvement Activities
Using sensing technologies, we visualize change points to discover abnormalities in production processes. Combined with AI-based shipping inspections, these sensing technologies have help to improve our preventive activities, which seek to eliminate defective products.
In FY2023, we launched the Global Quality Control Consortium, where employees in charge of quality control at overseas consolidated subsidiaries discuss quality control methods with each other. Discussing about the activities of each site helped to improve the level of quality control for the Group as a whole.
In FY2024, we will conduct activities to promote the automation of operations related to quality and shipping inspections as well as standardization using data so that we can provide products that have even less quality deviation.
Improvement of Product Safety
Product safety is the responsibility of manufacturers, and we have kept this in mind since RIKEN TECHNOS was established. We are further enhancing our product safety measures and complying with the Japanese Product Liability Act. We have not had a single product liability issue with any of our products for which product liability is a special concern (our products for medical use or our products which have received public certification, such as UL certification).
The Product Safety Committee conducts activities to identify and reduce our risks, including compliance with the Product Liability Act and management of chemical substances. In addition to products for which product liability is a special concern, cases that the overseeing department or the committee sees the need for risk identification and reduction are discussed by the committee to improve product safety.
