R&D
Topics
Here, we introduce RIKEN TECHNOS’s R&D topics and track record.
Commencement of Operation of the Semi-Commercial Plant for Manufacturing Thermoplastic Vulcanizate (TPV) as a Substitute for Cross-Linked and Vulcanized Rubber (December 13, 2023)
The final disposal ratio of scrap rubber was 18.5%, ranked second* following cinders among all types of industrial waste in FY2021. To expand efforts towards a circular economy that highlights resource and energy sustainability, among other purposes, there are high expectations that TPV (a dynamic crosslinking thermoplastic elastomer) with excellent recyclability will be a substitute for cross-linked and vulcanized rubber.
*Source: Report of FY2022 Survey on the State of Discharge and Treatment of Industrial Waste (FY2021 preliminary figures)
A semi-commercial plant (SCP) for TPV production has started its operation in the R&D Center (Tokyo) to develop TPV compounds as cross-linked and vulcanized rubber substitutes. Equipped with a small line with an annual production capacity of 100 tons, this SCP is suitable for scale-up testing, sampling and validation as per customer demand, and small-scale production. Accordingly, it is advantageous to satisfying customers’ special needs and promoting the development of high-end products that can be manufactured without occupying the full-scale capacity of our mass-production line. In this SCP, we are engaging in the development and validation of TPV compounds and planning to launch TPV compounds we developed for automobile molding parts and construction materials. We are also considering manufacturing sheets made of TPV compounds to market them as rubber substitute sheets.
Development of Reform Materials for Recycled Rigid Polyvinyl Chloride (PVC) (November 30, 2023)
Rigid PVC, which excels in rigidity, chemical resistance, and durability, is used for a variety of parts and materials, such as those for construction. While being equipped with these excellent properties, crushing molded rigid PVC for reusing sometimes ends up with insufficient thermal stability and melting, which may lead to degradation of appearances or physical properties of molded products. There thus remain challenges in recycling rigid PVC.
Focusing on the challenges, we endeavored to develop—by utilizing our knowledge of compound formulations technologies—reformers to add to recycled rigid PVC materials. Adding the products we developed to recycled materials decreases extrusion loads, enabling the production of molded products with stable appearance and uniform size. Products in multiple grades are available depending on the purpose of use such as decreasing extrusion loads, stable molding, and reinforcing impact strength.
【Properties of the Developed Products】
- Decrease extrusion loads during molding
- Expectation of producing molded products with better appearance and in uniform size
- Products to reinforce impact strength are also available
Commencement of Joint Research with Waseda University on Effective Utilization of Chlorine-Containing Plastics (June 29, 2023)
Efforts to develop waste plastic recycling methods have become active in recent years from the viewpoint of resource cycling. With chemical recycling, accompanied by degradation reactions, waste plastics are reduced to raw chemical materials in principle, thus enabling conversions to a variety of products with a wider scope of applications. Polyesters and polyolefins are major types of plastics currently being the subject of recycling method development. Some demonstrations are ongoing in pilot plants, and it is expected to be put into practical use soon.
PVC, which contains chlorine in the polymer skeleton, is regarded as being harder to recycle than the above-mentioned types of plastics because of the handling of chlorine-containing compounds generated through degradation reaction and the complexity of the residue skeleton that comprises mainly carbon. PVC compounds melted and kneaded together with additives—such as plasticizers, stabilizers, and fillers—are frequently used as raw materials for molded PVC products. The effects of these additives on degradation reaction are rather unknown. There are some cases of PVC recycling efforts to develop methodologies not to directly reduce it to vinyl chloride monomers but to convert PVC to other useful compounds. Most of these cases remain in the demonstration phase.
Recognizing the difficulty of establishing chemical recycling technologies for PVC and aiming to effectively utilize it, we start developing technology to recover useful metals from waste metal compounds using chlorine-containing plastics jointly with the research team of Prof. Chiharu Tokoro, Waseda University. Many waste metal compounds are oxide mixtures. By converting them into metal chloride, we can sort and recover useful metals utilizing steam pressure differences. This technology typically uses calcium chloride and such as the source of chlorine for chloride conversion. We use PVC and other chlorine-containing plastics as substitutes for chloride, aiming to effectively utilize these plastics.

As mentioned above, many of the PVC products in use contain various additives. It is thus necessary to consider effects brought by these additives to chloride reaction and the metal recovery process. In the joint research we launched, we will prepare PVC compounds that represent PVC products in use in society, and the team at Waseda University will consider how to optimize metal chloride conversion reaction using PVC compounds we prepared.
Development of a New Two-Dimensional Material Processing Method using PVC Film by Joint Research with the University of Tokyo (February 28, 2023)
Two-dimensional materials, such as graphene and transition metal dichalcogenide, have an extremely thin sheet-like structure made of one atom. Their properties as a delaminated material are different from those of conventional materials. In particular, graphene excels at electronic and thermal conductivity by approximately 100 times those of silicon, and it is as strong and flexible as diamond. Accordingly, R&D activities are actively carried out to develop industrial applications of graphene in the fields such as next-generation ultrafast electronic devices, high-sensitivity sensors, and power-saving transistors.
On the other hand, graphene is hard to handle because it is extremely small and thin. The low success rate of graphene processing, such as moving it to the desired location and stacking sheet pieces, has been hampering accelerated research and practical use.
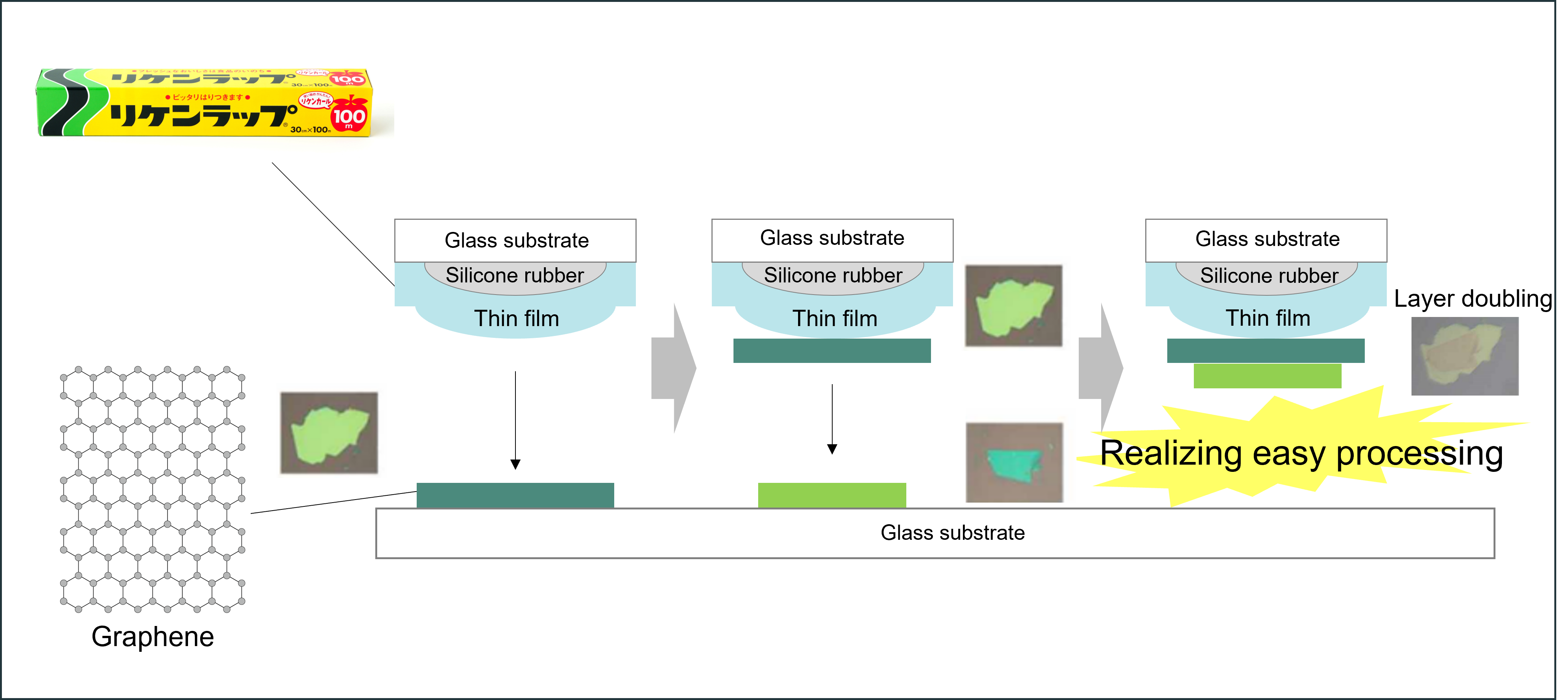
Having explored the potential of various materials for processing graphene pieces, the University’s laboratory found that our product “RIKEN WRAP” tends to increase the success rate of graphene processing. In response to consultation from the laboratory, we started joint research to identify the reason and to establish a processing method. While considering and validating film formulations using the PVC formulations and manufacturing technologies and film manufacturing technology, our company’s fundamental technologies, we analyzed delamination behaviors of graphene sheets to confirm that adjustments of temperature conditions during processing, among others, make graphene easier to handle.
By applying this processing method to combine two types of PVC films, flipping over compound atomic layers made of multiple two-dimensional materials—such as graphene and hexagonal boron nitride—became easily possible. As such a flip-over processing method is conventionally difficult, this technology is critical to the realization of various layer combinations and processing and development of next-generation semiconductor devices and switching circuits. The above-mentioned research outcome is published in “Scientific Reports” [Scientific Reports volume 12, Article number: 21963 (2022)].
Addition of a New Series to Our Biomass Plastic Product “RIKEBIO®” (December 7, 2022)
A new series “Natural RIKEBIO®” was added to our biomass plastic product lineup RIKEBIO®. Natural RIKEBIO® aims to reduce waste by using our original formulations and manufacturing technologies to compound natural resources that would otherwise be discarded, and effectively utilize them as molding materials. Using polypropylene (PP) as the base material, the natural resource content can be elevated up to 60%, reducing petroleum-derived plastic content. Our Natural RIKEBIO® is expected to contribute to reduced plastic use and no plastic use.
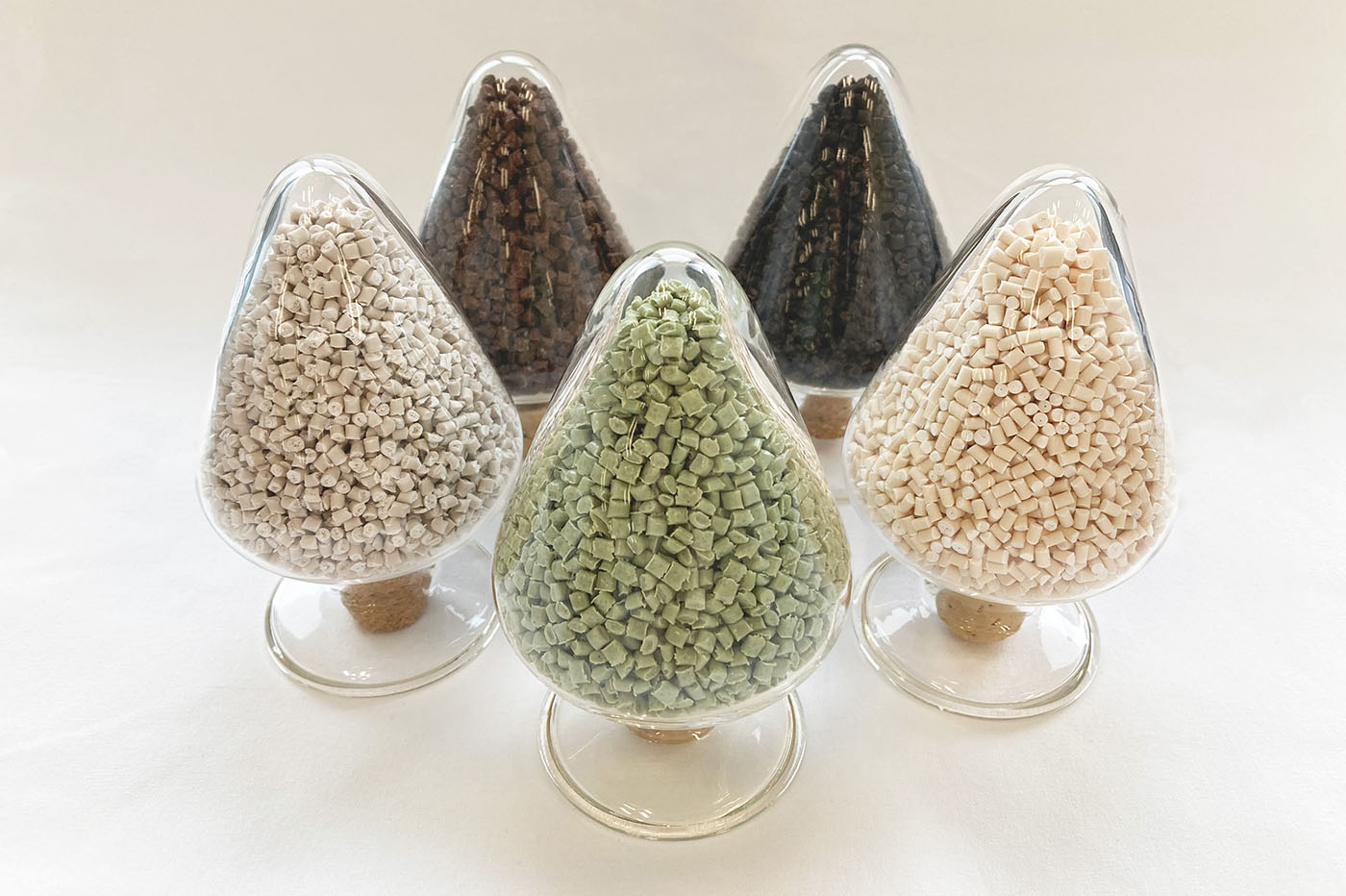
Natural resources that are discarded comprise thinned wood and other forestry resources, agricultural resources including tea and rice husks, and fishery resources including shells. As these items are often produced and consumed locally, their procurement requires compact transportation networks, which leads to reduction of environmental load.
We can customize as per customers’ requests the volume of natural resource additives to obtain finely tuned texture and coloring.
In addition to PP, additions to polyvinyl chloride resin (PVC) or thermoplastic elastomer (TPE) are possible. We provide our customers with waste reduction solutions equipped with the original properties of natural resources as well as added new value that fits with usage. Natural RIKEBIO® compounds are suitable as molding materials for extrusion and injection molding. We are also exploring the possibility of developing Natural RIKEBIO® sheets by applying our film manufacturing technologies.
【About RIKEBIO®】
The biomass content of RIKEBIO® compounds is elevated by adding biomass-derived plasticizers and fillers. We have a lineup of PVC and TPE products and some grades have acquired the Biomass Mark*. As per our customers’ requests, the biomass content is adjustable to develop grades that can obtain the Biomass Mark.
RIKEBIO® compounds are sustainable and practical products, as they can be applied to extensive purposes with performance levels on par with conventional petroleum-derived products. They are establishing a track record through their use in everyday items and industrial material hoses. Besides compound products, we are also developing biomass films and biomass wrap using RIKEBIO®.
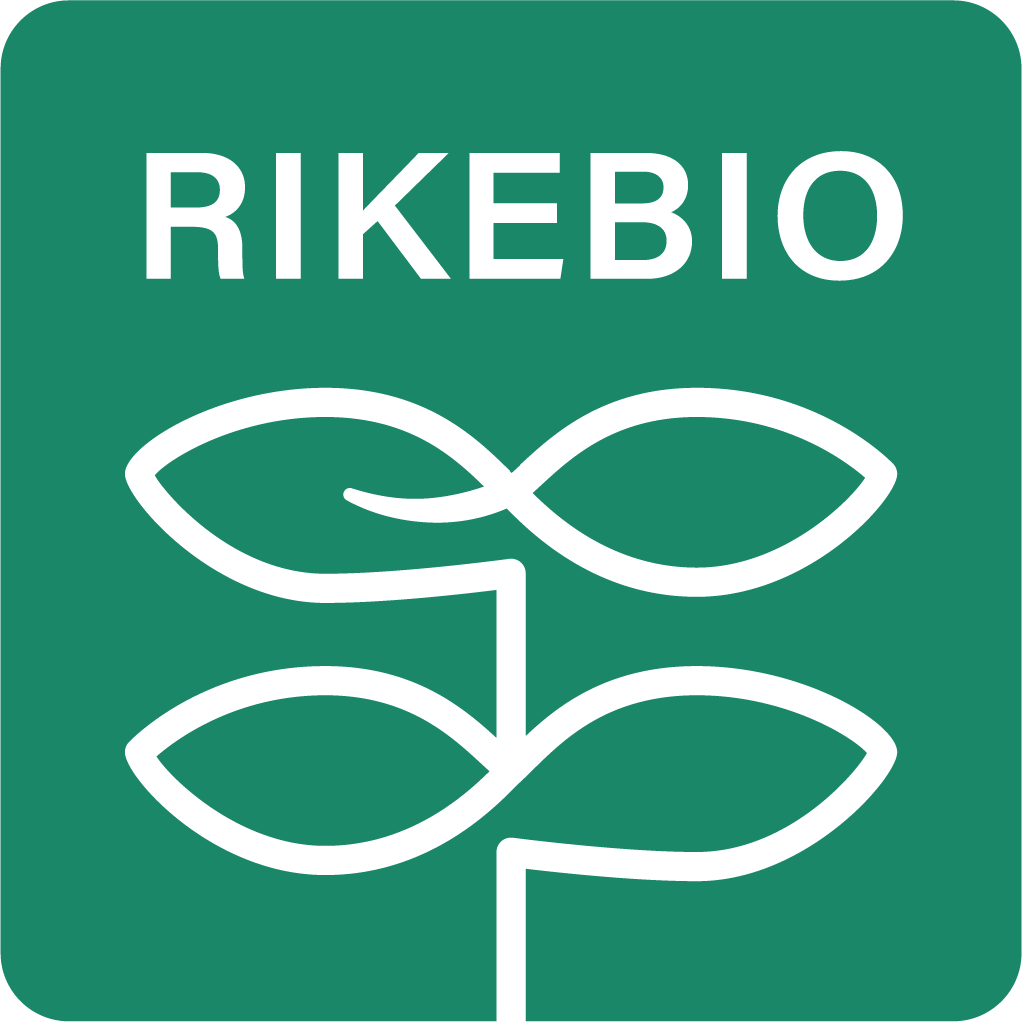
*The Biomass Mark is a symbol of environment-friendly products certified by the Japan Organics Recycling Association. The Biomass Mark is granted to products manufactured by utilizing bioresources (biomass) and equipped with quality and safety that conform to related laws, regulations, standards, certifications, etc. (Source : Website of the Japan Organics Recycling Association)
Development of an Environment-Friendly ACS Resin (November 16, 2022)
Our Group provides materials for products associated with power generation and transmission facilities in the industrial and infrastructure sectors.
ACS resin is a material with excellent moldability mainly composing acrylic (A), chlorinated (C), and styrenic (S) polymers. Although typical rigid flame-retardant resins are known for significant weathering deterioration, ACS resin’s weather resistance is superior to those of other flame-retardant resins. It can be used with white-colored tones and excels at electrical properties as well. Being a rigid resin that is heat- and climate-resistant, ACS resin has a rich track record with housing, industrial meter mounting boards, smart-meter housing, fire alarms, etc.
ACS resin has excellent properties, but some of its additives contain organic tin compounds. Plastic products containing organic tin compounds are subject to laws and regulations in some countries. Accordingly, ACS resin sometimes does not conform to the green procurement standards of companies.
Recognizing this issue, we developed a new environmentally friendly ACS resin by successfully removing the tin content without damaging ACS resin’s excellent functionality. We will carry out sample work to explore its potential in the electrical material and other broader sectors.
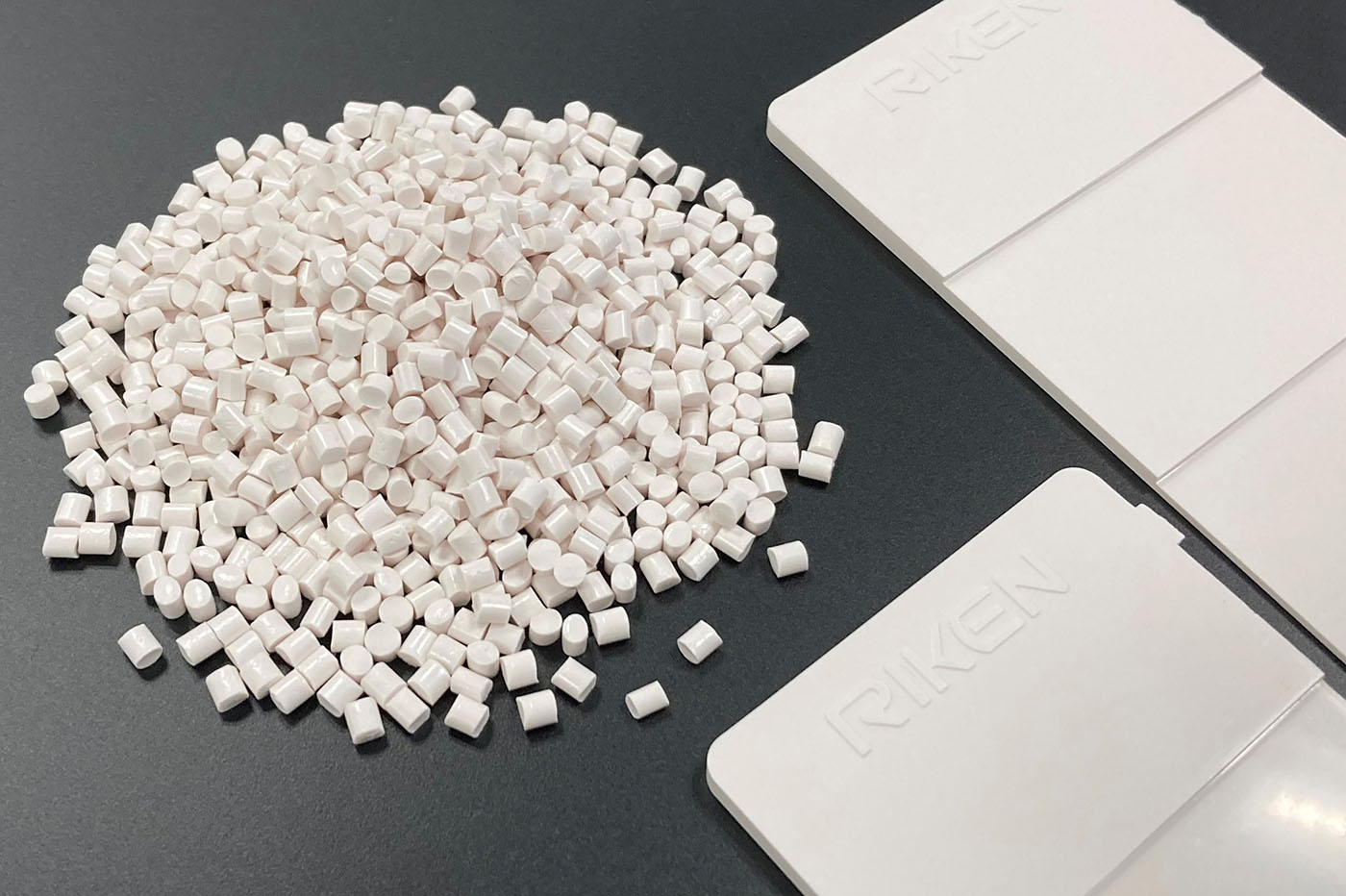
Market Launch of our Biomass Plastic Product “RIKEBIO®” (June 13, 2022)
Plastic products produced by unique formulations and manufacturing technologies of our Group have been supporting industries, improving quality of life, and creating a safe, affluent society since our establishment. Concurrently, as part of our responsibility as a chemical manufacturer to contribute to achieving a sustainable society, RIKEN TECHNOS is developing products that use renewable biomass materials.
We started sample work of the biomass-based products in 2019 and just launched them under the RIKEBIO® brand.
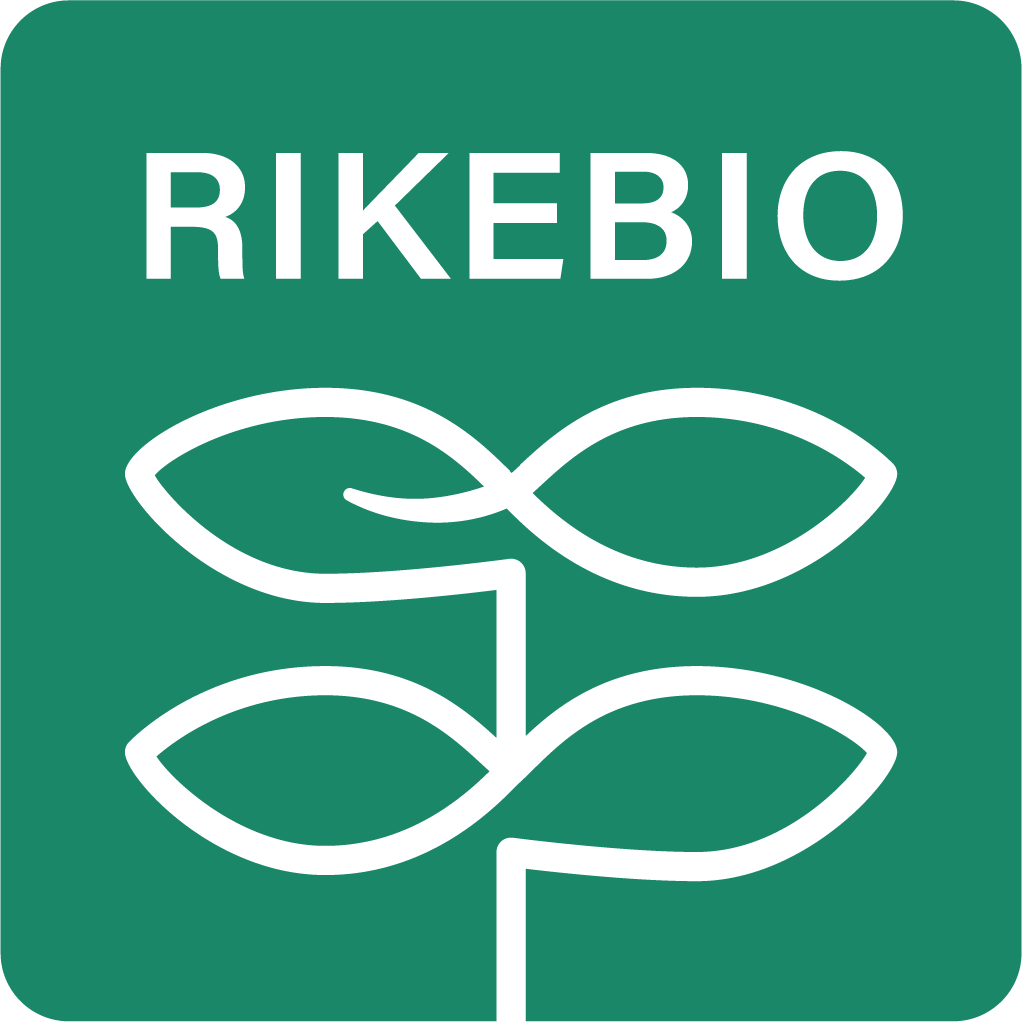
1. Soft PVC RIKEBIO® Compounds
The main raw material is PVC resin and 57% of it is derived from salt, a natural material. Compared to other resins, such as polyethylene and polypropylene, composed almost entirely of petroleum, it contains less petroleum-derived content.
Furthermore, the biomass content of compounds is elevated by adding biomass-derived plasticizers and fillers. The Biomass Mark* for 40% biomass content is granted to RIKEBIO® “RB-VE70C1.” Our products’ quality and functionality are equivalent to those of soft PVC compounds for general purposes.
2. TPE RIKEBIO® Compounds
We have products with biomass content of from 10% to 30% for use in a broader range of rigidity. Similarly to soft PVC, our products are equipped with quality and functionality equivalent to regular TPE compounds. Having excellent recyclability of TPE and partially using biomass materials, these products contribute to waste reduction.
We offer multiple types of soft PVC and TPE RIKEBIO® compound products for broad uses such as automobile parts, consumer goods, building interior materials, and civil engineering materials.
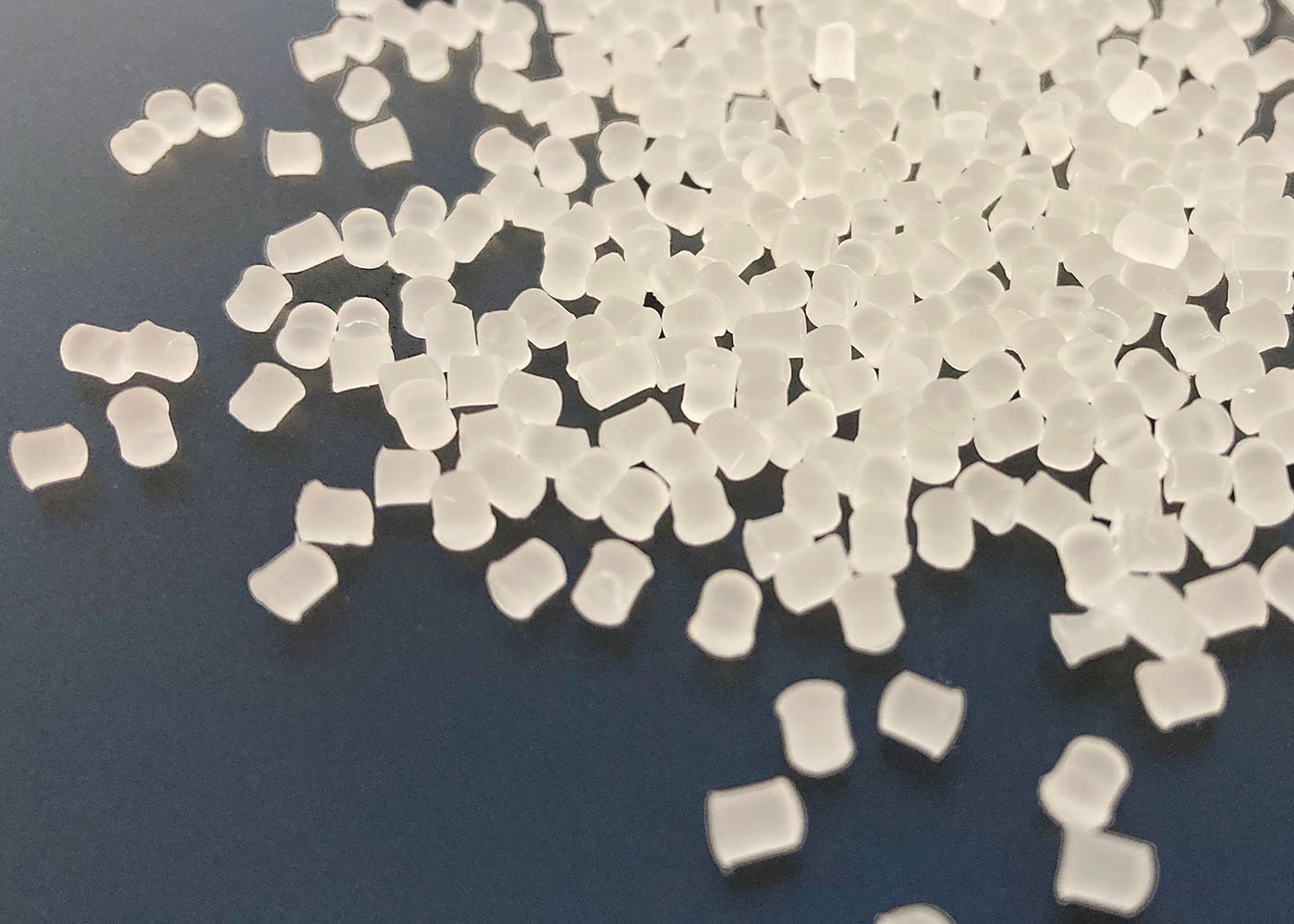
Utilizing the RIKEBIO® compound technology, we are also developing biomass films.
3. Semi-rigid PVC RIKEBIO® Film
This semi-rigid film product series is widely used with building interior and exterior finishing, labels, stickers, automobiles, etc. Biomass is used in the base material film. We can propose it as an environmentally friendly product with 10% to 20% biomass content that functions as same as conventional products.
4. PE RIKEBIO® Film
This product series is PE biomass olefin films with 20% to 40% biomass content. We can propose thin, highly concealable products with high-printing properties by utilizing the RIKEN TECHNOS Group’s strength, the formulations and manufacturing technologies.
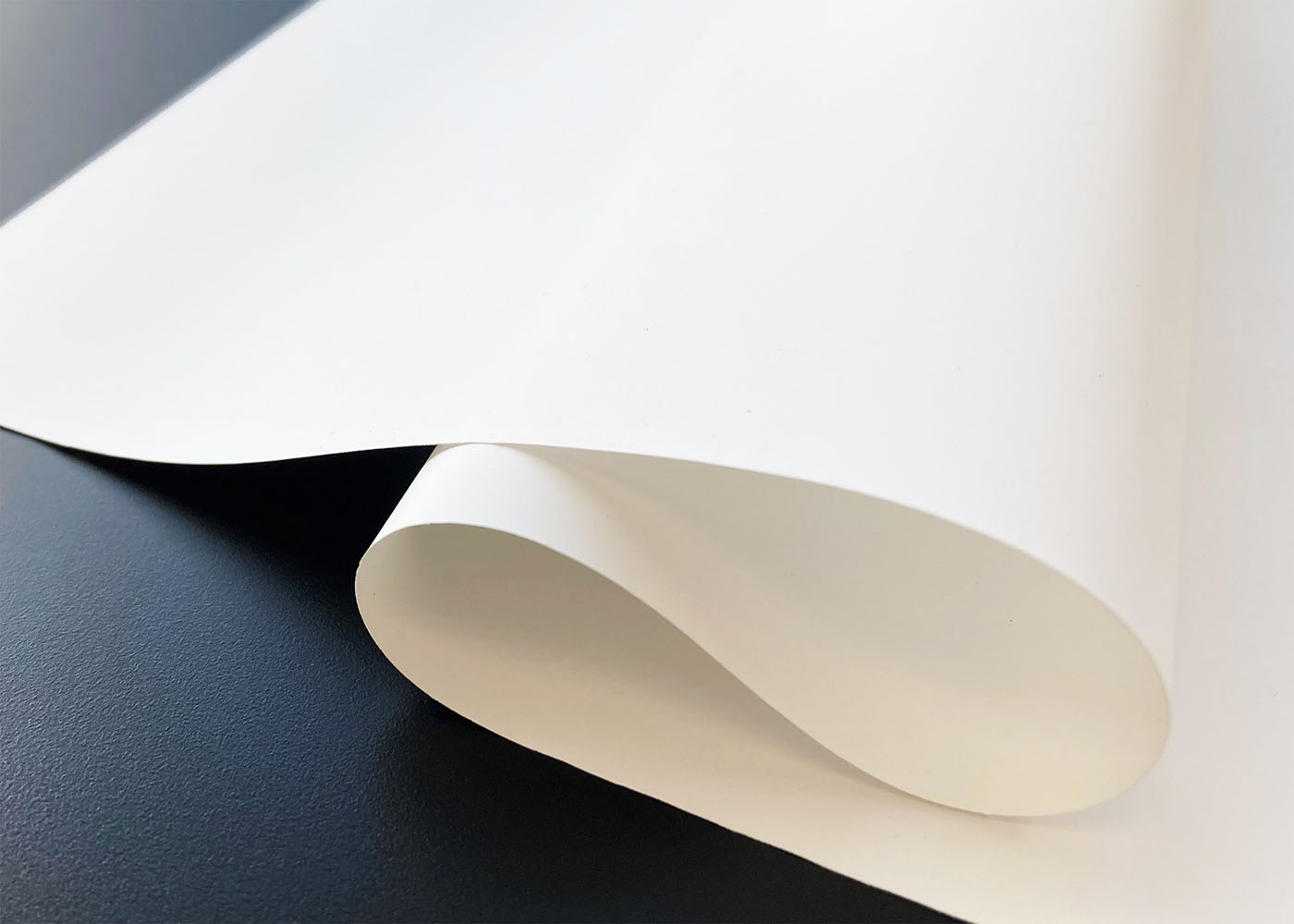
RIKEBIO® products are sustainable and practical and serve extensive purposes. We can obtain the Biomass Mark for both RIKEBIO® compounds and RIKEBIO® films as per customers’ requests.
*The Biomass Mark is a symbol of environment-friendly products certified by the Japan Organics Recycling Association. The Biomass Mark is granted to products manufactured by utilizing bioresources (biomass) and equipped with quality and safety that conform to related laws, regulations, standards, certifications, etc. (Source : Website of the Japan Organics Recycling Association)