Sustainability
Materiality Topics
We identify important topics as materiality toward realization of the long-term vision, reflecting considerations such as the medium- to long-term conditions of the Group’s business environment, social issues, and the needs of stakeholders.
Amidst a drastically changing business environment the Group has been working to achieve its long-term vision, “aiming to become the leading provider of comfort for all living spaces” since 2016, and has formulated a medium-term business plan and strategy, and is implementing a variety of measures.
The long-term vision incorporates the concept of delivering optimal solutions (comfort) through our businesses to “all living spaces,” including those areas of society we will become involved with in the future, in addition to existing business areas and stakeholders.
The RIKEN TECHNOS GROUP recognizes that responding to issues surrounding sustainability is important. By incorporating these issues into our management, we seek to help realize a sustainable society and enhance our enterprise value.
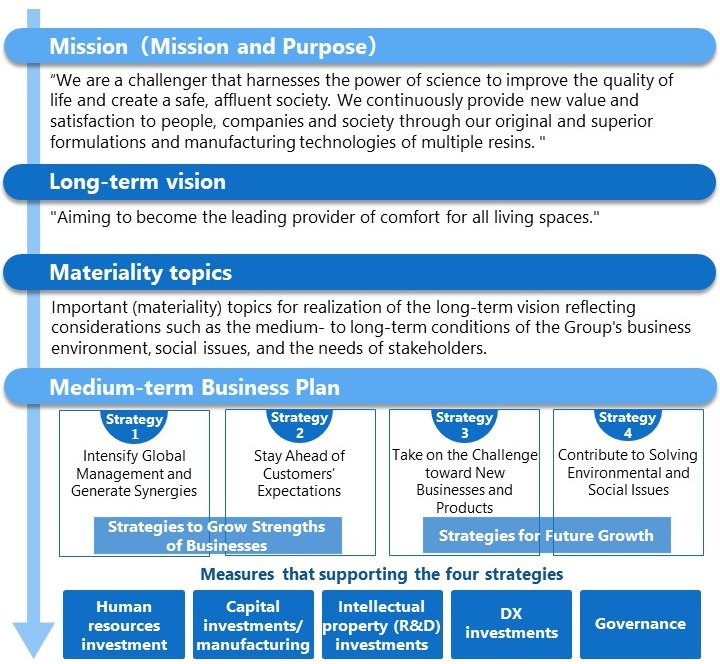
Process of Identification of Materiality Topics
Materiality topics were identified through companywide discussion of topics that should be addressed, based on analysis and review of changes to the Group's business environment, social issues, and stakeholder needs. The Sustainability Committee manages the progress on materiality topics identified.
Step 1: Reviewing environmental changes, social issues, and stakeholder needs
The Sustainability Committee secretariat, whose membership consists of representatives of individual divisions, played a central role in identifying relevant key topics with reference to various guidelines, key performance indicators (KPIs), and other information regarding the Sustainable Development Goals (SDGs), the environment, society, and governance (ESG), and other topics, to review medium- to long-term changes to the Company's business environment, social issues, and needs of stakeholders and others.
Step 2: Candidate selection
Candidate materiality topics for the Group to address were selected based on the key topics identified in Step 1.
Step 3: Candidate evaluation
The candidate topics selected were assessed for materiality along the two axes of importance to the Group and importance to stakeholders.
Step 4: Deliberation by management
Roundtable discussions were held among Directors and executive officers for identification of materiality topics by management, including outside Directors. Participants discussed the individual candidate materiality topics and their importance.
Similar discussions were held in roundtable talks by department managers and those in equivalent posts.
Step 5: Matrix preparation and approval by management
Based on the details of the discussions above, the Sustainability Committee revised and made additions to candidate materiality topics and prepared a materiality matrix.
Step 6: Approval by management
The materiality topics identified was approved by the Board of Directors.
Materiality Matrix
The importance of candidate materiality topics was evaluated, and those with high importance to both RIKEN TECHNOS GROUP and stakeholders were identified as materiality topics.
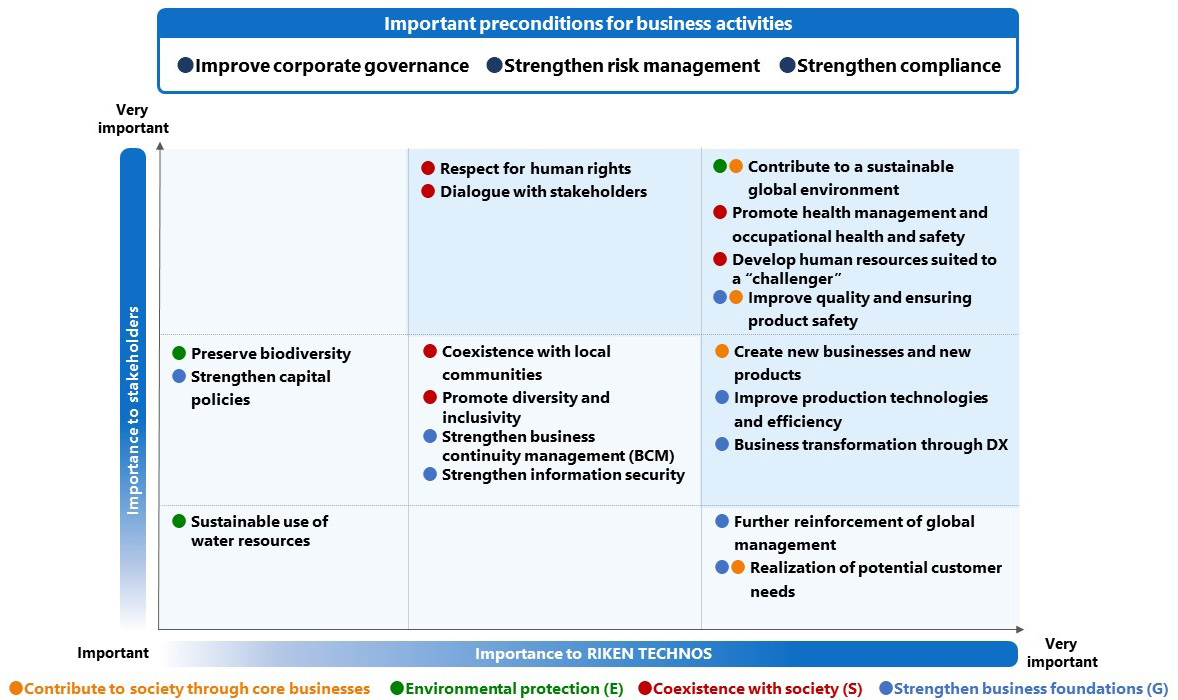
Materiality Topics and KPIs
From the materiality topics identified, the Group established the following nine indicators and targets (KPIs) of particular importance to the Group. We will strive to realize the long-term vision by repeating the plan-do-check-act (PDCA) cycle and by promoting efforts to achieve our targets and managing the progress of these activities.
Materiality Topics | Standards for Evaluation (KPIs) | Results | Medium- to Long-term Targets | Relevant SDGs | |
---|---|---|---|---|---|
FY2022 | FY2024 | FY2030 | |||
Contribute to a sustainable global environment | Achieving CO2 emissions reduction targets for 2030 (non-consolidated) | 41,139 t | 35,446 t | 24,139 t (46.2% decrease compared to FY2019) |
![]() ![]() ![]() ![]() ![]() |
Carbon neutral by 2050 (Group) | 86,220 t | - | - | ||
Ratio of total waste to total production (non-consolidated) | 3.44% | 3.3% or less | 3.0% or less | ||
Promote health and productivity management | Occupational injuries requiring time off work (domestic)*1 | 0 | 0 | 0 |
![]() |
Percentage of employees undergoing specified health examinations (domestic) | 88.9% | 90% | 90% | ||
Percentage of employees provided specified health guidance (domestic) | 52.5% | 55% | 60% | ||
Develop human resources suited to a “challenger” | Training cost per employee (non-consolidated) | 45,000 yen | 117,000 yen | 140,000 yen |
![]() |
Improve quality and ensuring product safety | Serious quality incidents requiring recalls (non-consolidated) | 0 | 0 | 0 |
![]() ![]() ![]() |
Serious violations of legal and regulatory compliance regarding use of chemical substances (non-consolidated) | 0 | 0 | 0 | ||
Create new businesses and new products | Numbers of patents applications (non-consolidated) | 8 | 45 (cumulative) (FY2022–2024) |
210 (cumulative) (FY2022–2030) |
![]() |
Numbers of collaborations with external parties (non-consolidated) | 4 | 10 (cumulative) (FY2022–2024) |
35 (cumulative) (FY2022–2030) |
||
Improve production technologies and efficiency | Production capacity (non-consolidated) | -3% (vs. FY2021) |
+10% (vs. FY2021) |
+33% (vs. FY2021) |
![]() ![]() |
Business transformation through DX | Development of Ml human resources (non-consolidated) | - | 9 persons | 20 persons |
![]() |
DX training for all employees (non-consolidated) | - | 100% attendance | 100% attendance | ||
Respect for human rights | Human rights and compliance training for all employees (domestic) | 60%*2 | 100% attendance | 100% attendance |
![]() ![]() ![]() ![]() |
Conduct ESG survey to suppliers (non-consolidated) | Once | Once | Once | ||
Dialogue with stakeholders | Meetings with investors and existing shareholders (non-consolidated) | 104 companies | 140 or more companies/year | 200 or more companies/year |
![]() ![]() |
Conduct satisfaction survey to customers and suppliers (non-consolidated) | Once | Once | Once |
*1Industrial Accidents which require the sending of a worker casualty report
*2Calculated based on the number of attendees for compliance training, including training on discrimination and harassment (excluding attendees of on-demand training)